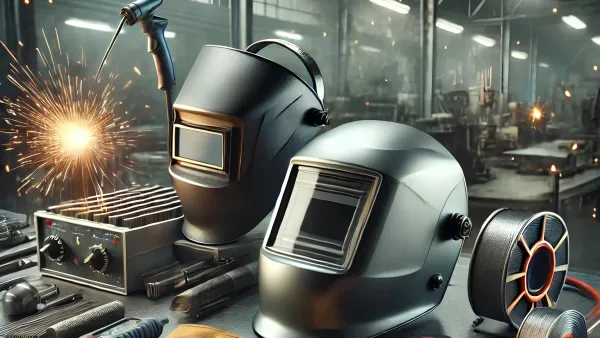
Top 10 Essential Welding Tools for Beginners
Welding is a skill that combines craftsmanship with precision, enabling the creation and repair of countless metal structures. If you're just starting your journey in welding, having the right tools is crucial for success and safety. Here's a list of the top 10 essential welding tools